Tucked away on an idyllic semi-rural site in Paremoremo, on the outskirts of Auckland, New Zealand’s first — and the southern hemisphere’s largest — 3D-printed concrete house marks a bold move forwards, and a golden opportunity to make architecture more accessible.
Standing on this site, surrounded by mature gum trees and looking over a private wetland, you could very well be somewhere in the northern New South Wales hinterland. It was no doubt this feeling of geographical ambiguity, along with the seclusion and privacy the land affords, that the owners were first intrigued with when they decided to purchase it for their next building project — one that would be designed as a place for their teenage children to enjoy their last years living at home, and as a ‘forever’ home for the couple.
So, after a 10-year hiatus between projects, a client-architect team was reunited to form a concept of considerable creativity. The budget wasn’t high, and the brief revealed a desire for a home that had the hallmarks of innovation that underpinned the work of the father of one of the clients — an English architect who was well known for his colourful postmodern buildings.
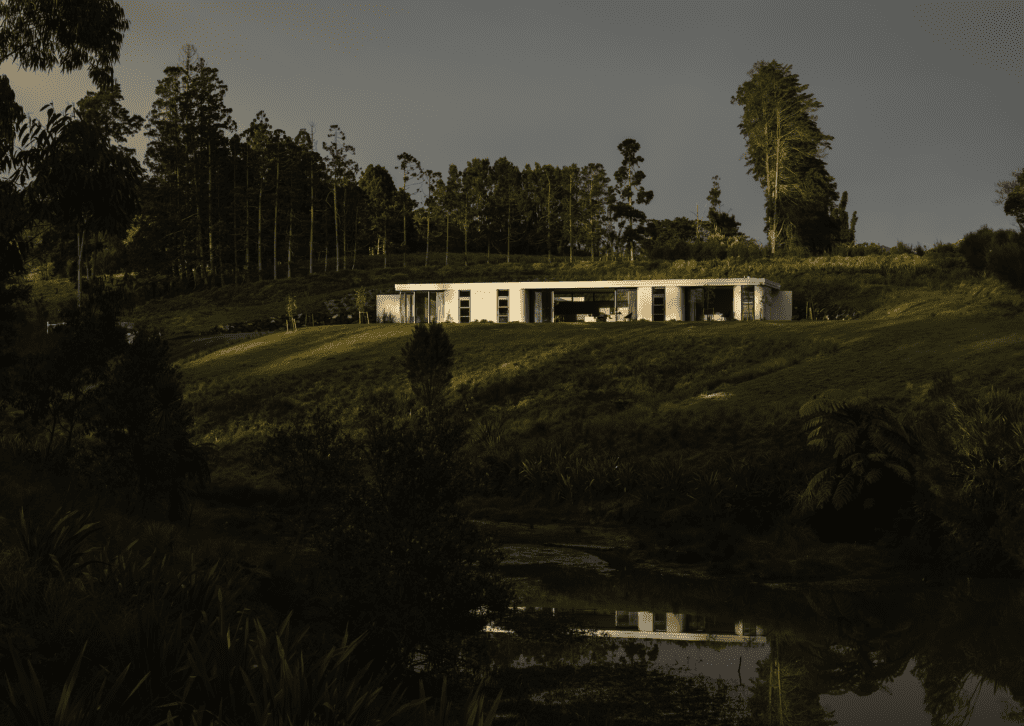
A low-slung pavilion was the early concept, and the initial iterations of the design considered a concrete block form — a decision based on budget constraints and ease of construction. During the design phase, architect Tim Dorrington of Dorrington Atcheson Architects (DAA) came across a technology new to New Zealand, and one that had never been utilised for an entire house: 3D concrete printing.
“Prior to this, it had only been used in New Zealand to create internal walls, so, when we found and tested the technology, the clients made the brave decision to be guinea pigs as we embraced the methodology to design and build New Zealand’s first 3D-printed house.”
It’s a technology that has been aggressively embraced overseas to address housing affordability; the technology allows for precise and efficient on- or off-site printing, reducing the cost of labour and time required on site. Combine that with the fact that the insulated 3D-printed concrete panels form the entire structure — from the external wall to the finished internal wall linings — thereby reducing the number of materials required to build a high-performing, energy-efficient home, and you have a compelling case for 3D-printed homes in the future.
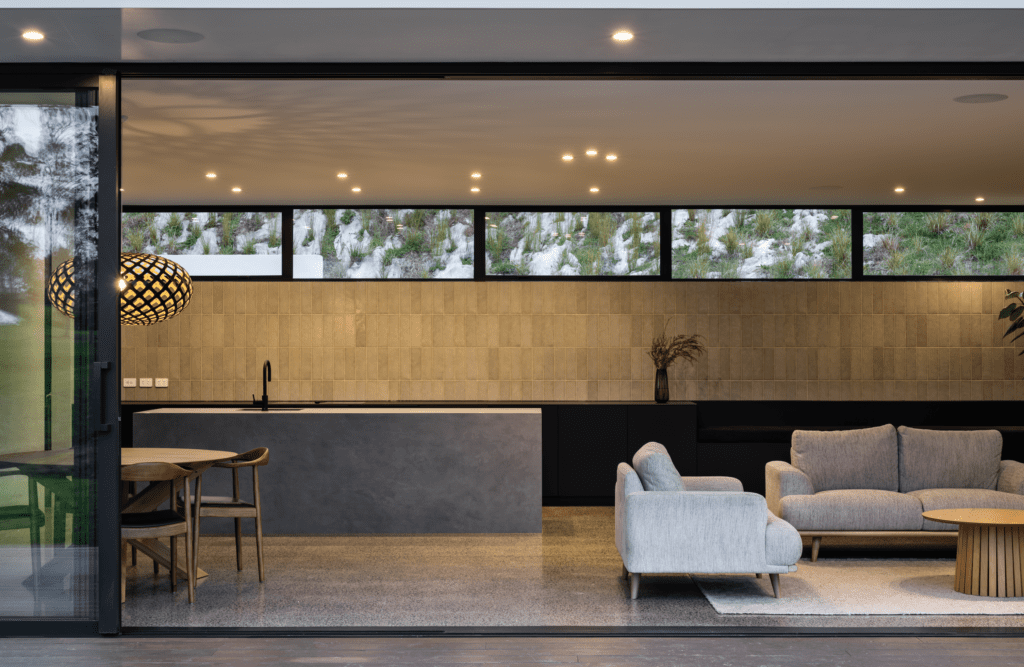
In this build, the technology has contributed to an architectural home that rivals the per square metre cost of a group-home-build property, Tim tells us. It’s something DAA is firmly committed to: the notion that architecture, when considered, can and should be delivered across budget and scope.
Facing north, the home is perched on a flat part of the otherwise sloping site overlooking the wetland. There are a smattering of other houses around, but none close enough to feel as if there are immediate neighbours. It’s a quiet place; a peaceful retreat from city life.
Inside, that quietness is abounded with spaces that seem to flow effortlessly into one another in a subtle linking of form and function. That’s achieved in part due to the 3D-printed walls, which curve and meander around nooks and rooms, encircling, and suggestive of movement, openness, and enclosure.
“The extruded 3D-printed panels allow you to achieve shapes and forms you wouldn’t otherwise be able to create without going to a lot of trouble — in fact, printing curves is much easier than right angles,” Tim tells us.
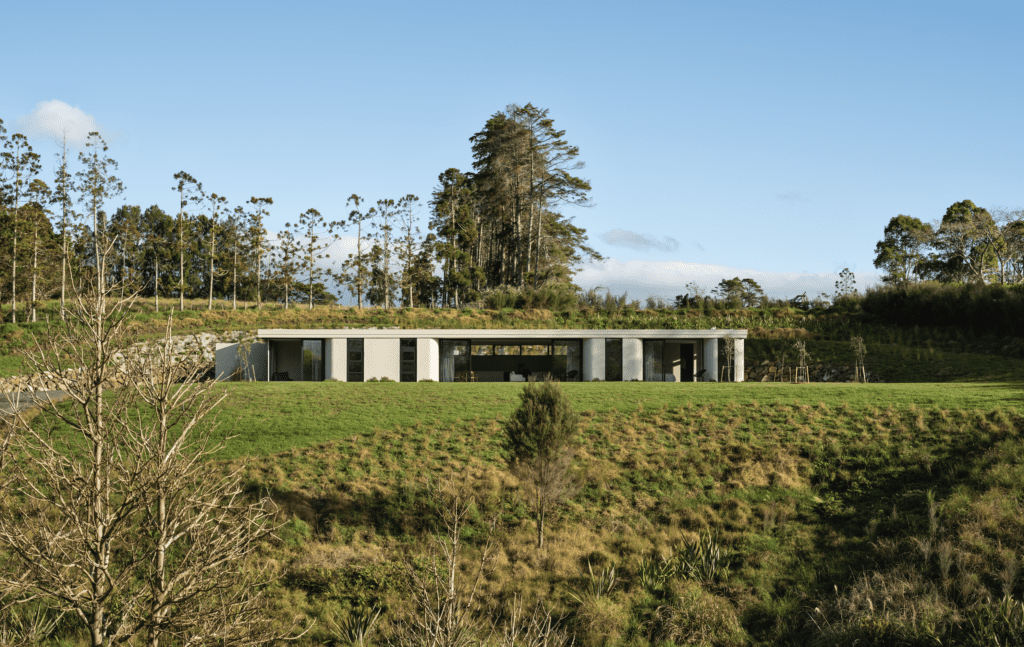
The plan is simple. In the centre, a large open-plan kitchen, living, and dining area is bookended on each side by private bedroom nooks — at one end, the owners’ retreat, with a simple but alluring en suite framed by curved walls; at the other, the children’s bedrooms, and another bathroom, along with a second lounge that occupies the north-eastern end of the house. Here, the glazing peels away to allow the room to open on two sides, effectively forming a transient space between indoors and out.
The printed walls were finished with a Resene ROCKCOTE plaster system in a soft grey hue that further accentuates the ambiguity between spaces, forms, and the thresholds between inside and outside areas. As the light moves around the house, the soft texture of the plaster creates an unexpected warmth, the finish almost velveteen.
Looking forward, this technology may very well contribute to a new era of residential building in New Zealand. As it stands, this project offered the architect, manufacturer Qorox, and builder Senior Construction a host of valuable learning opportunities as the methodology was put to the test. There were speed bumps along the way, but the end result speaks for itself.
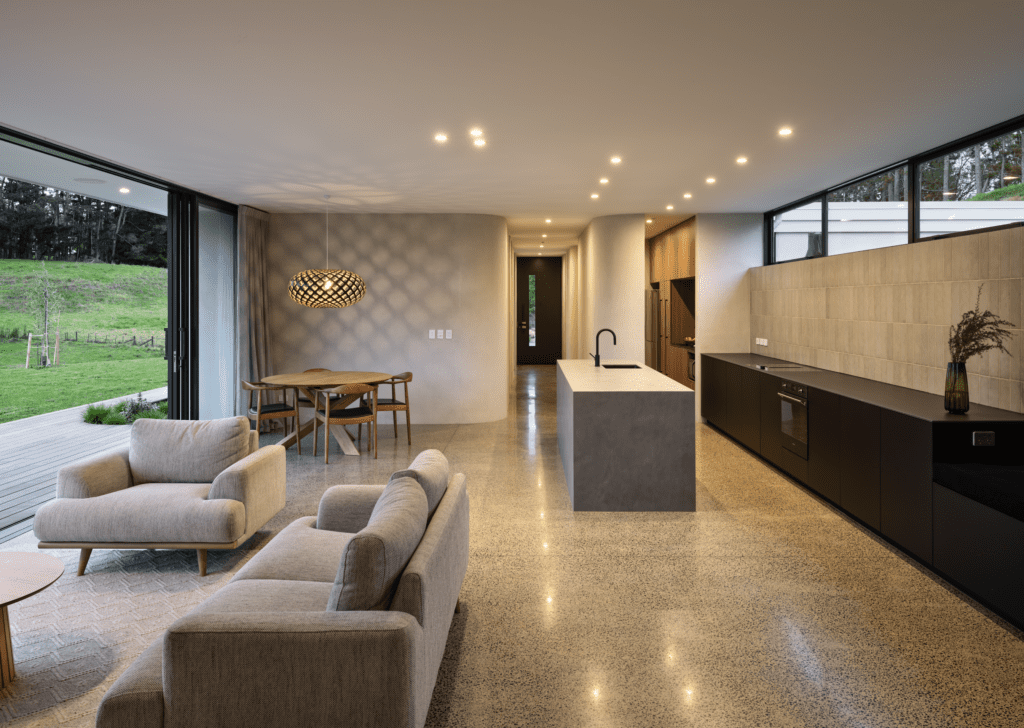
Qorox managing director, Wafaey Swelim, says DAA’s design enabled the Qorox team to utilise the full capabilities of their 3D concrete printer. “3D-printed concrete is the next evolution in building, and it’s happening right now, right here in New Zealand.”
“It’s a great idea,” Tim explains. “What you end up with, if it’s done carefully, are walls in place that form the external cladding through to the internal lining. By manufacturing off site, in theory, while the slab is getting poured, the finished wall panels could be installed, followed by the roof — and you very quickly have a weather-tight building. It speeds up the building process, lowers the cost of building, and should allow us to build bespoke architectural homes at an accessible price point.”
Words: Clare Chapman
Images: Simon Devitt