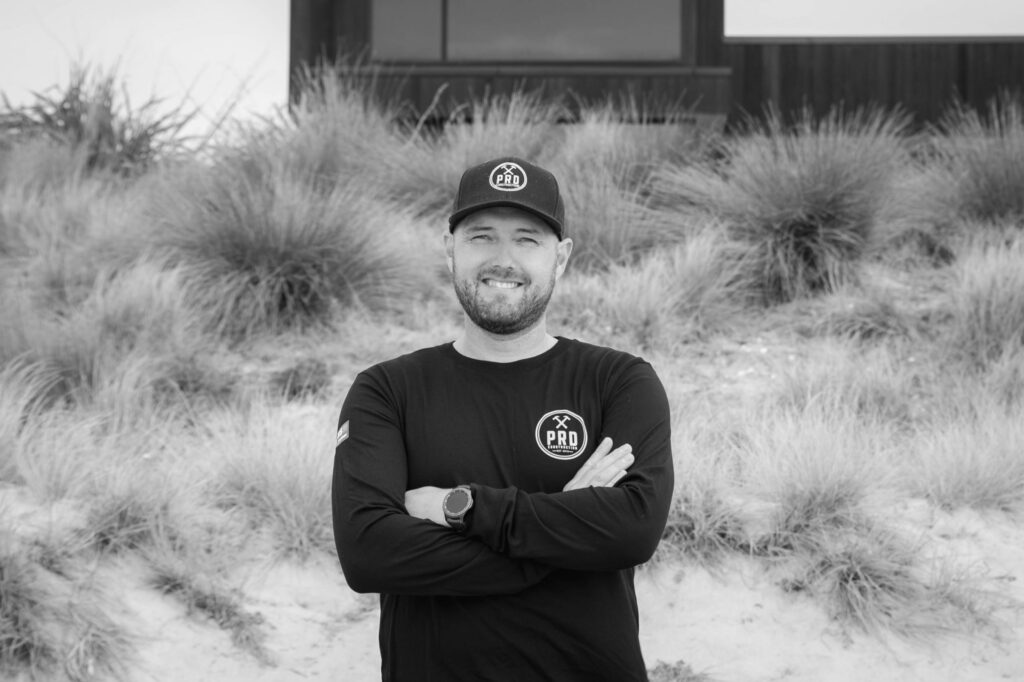
Balancing a beachfront site with a unique design presented PRD Construction with one of its more fascinating builds to date.
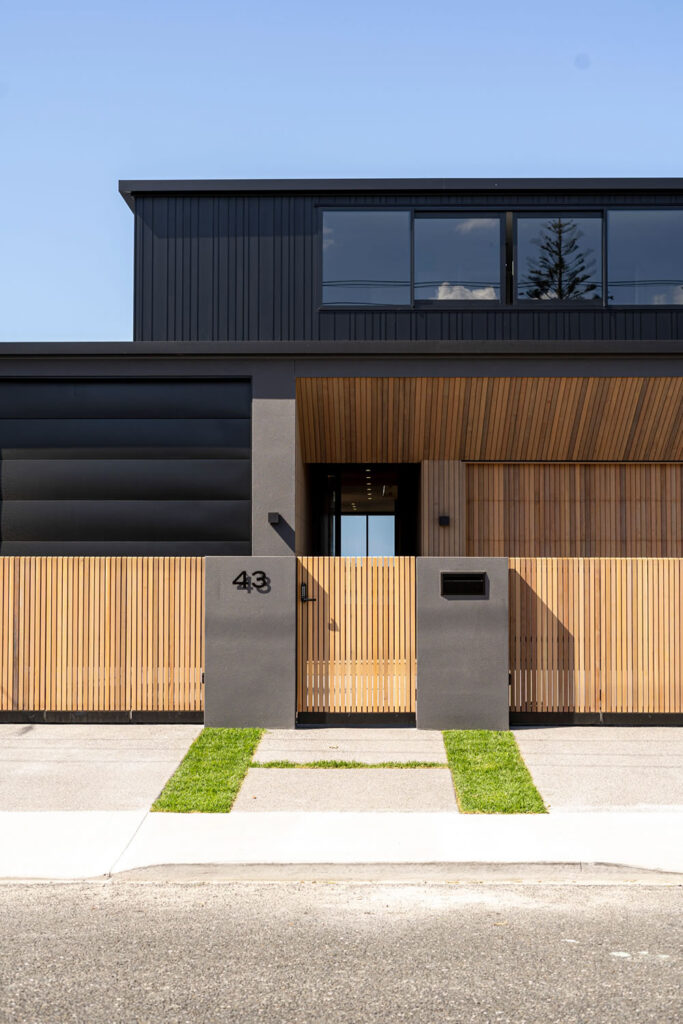
This Studio Brick-designed home on Papamoa Beach makes the most of its beachfront site with a long, linear plan across two storeys.
Given how close the site is to the coast, it required 120 self-driven piles for the foundation to be built on. “This was due to the soil conditions because, obviously, it’s all sand,” PRD Construction co-owner Paul Dent says. “There aren’t a lot of allowances, especially when a steel portal sits directly on the piles.”
Installing 14 tonnes of structural steel was no mean feat, craned in to support the home’s load. “Large steel portals and beams were required throughout the structure, even in the garage, to position the boat shed at the required height,” Paul says. “The home features a timber frame, but there is a large span where there are no walls in the middle to take the load; it’s all in the structural steel.”
Cranes accessed the site multiple times during the build, so one of the first challenges lay in a lack of road access due to existing power lines and the neighbouring homes close to the site.
“Fortunately, one of the neighbours allowed us to use their lawn to access the site,” Paul says. “We brought their lawn back to brand new with reseeding and supplied bottles of whisky!”
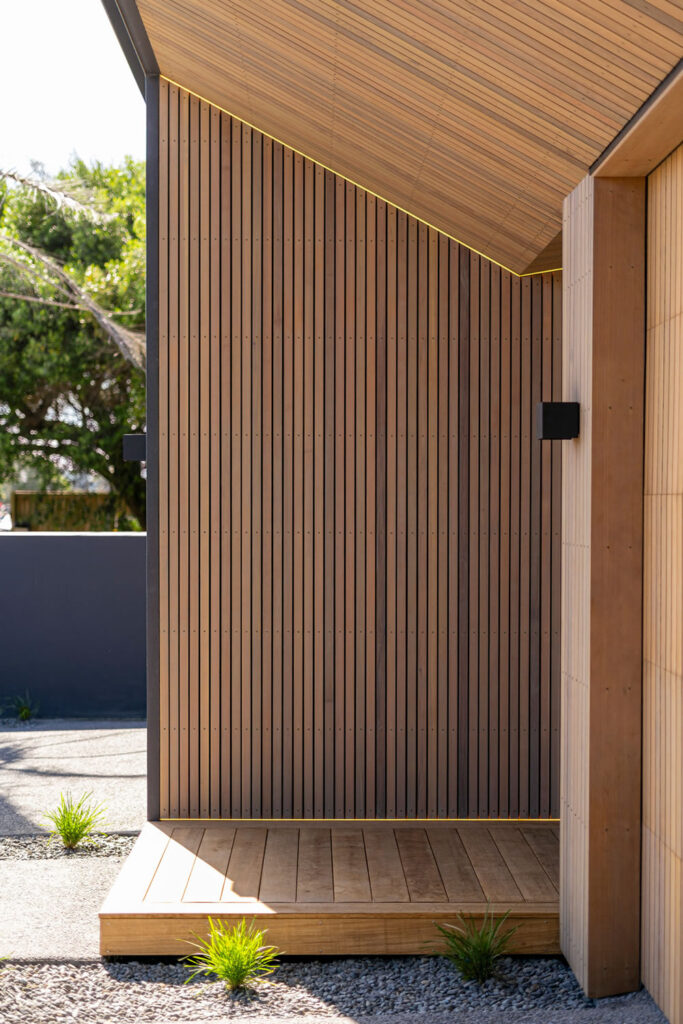
Aluminium cladding covers the exterior’s upper storey and the roof. “You get everything here; rain, wind, salt, and sun. Aluminium’s benefits are in the warranty, the look and how easy it is to clean. But it requires more preparation in the cavity battens with the build-up of back-flashings.”
In contrast, the lower storey is clad in cedar. “We pride ourselves on making everything perfect,” Paul says. “We focus on every little thing, even the individual boards matching on the garage door so the tones flow, for example.”
A hidden underfloor wine cellar was one of the more unusual challenges of the build, featuring a glass floor above it: “Its challenge was in dealing with a tight space late in the build,” Paul says. “We lifted it – an aluminium unit – in under the floor by hand.”
“Getting to build something on that scale was a massive opportunity for us,” Paul says. “Being involved in something with that amount of steel and using cranes on a large scale was fantastic.”
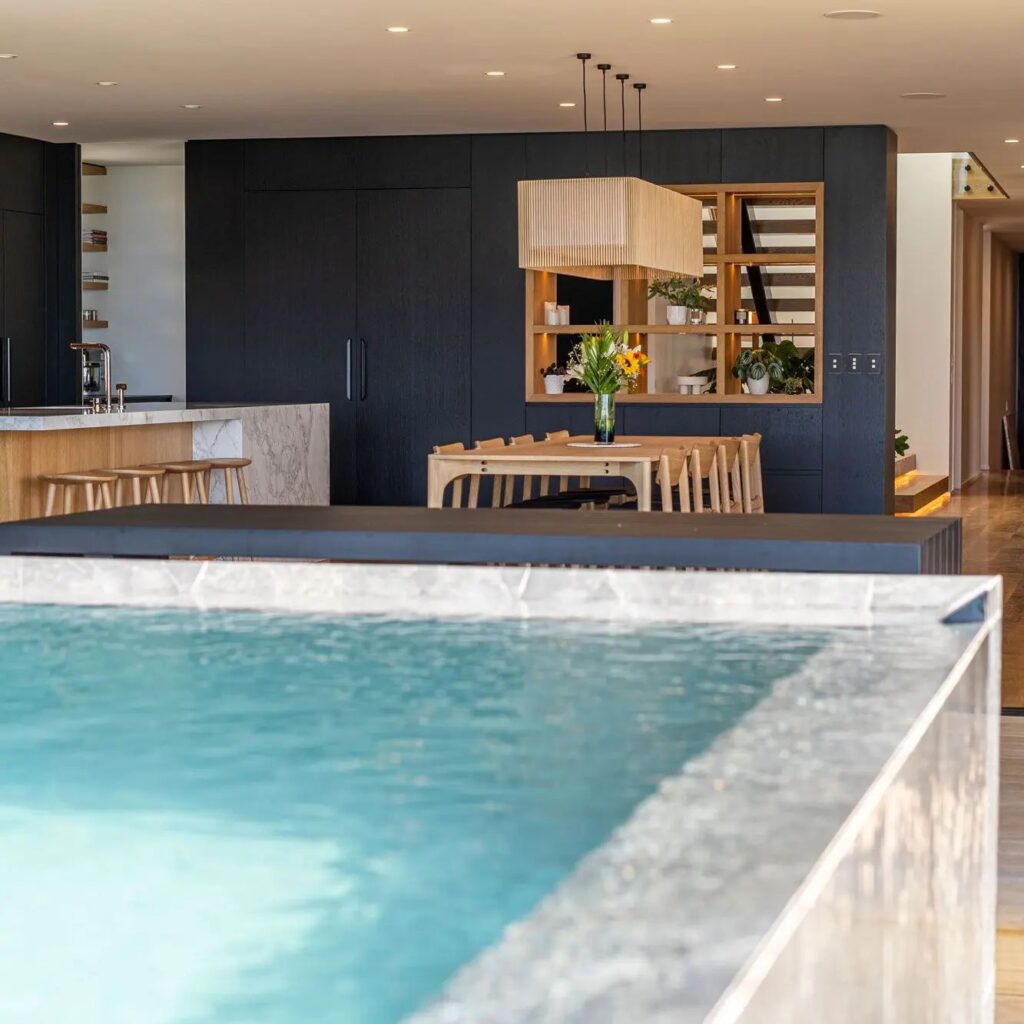